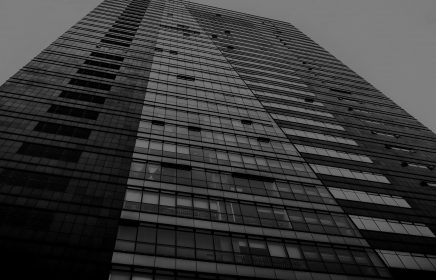
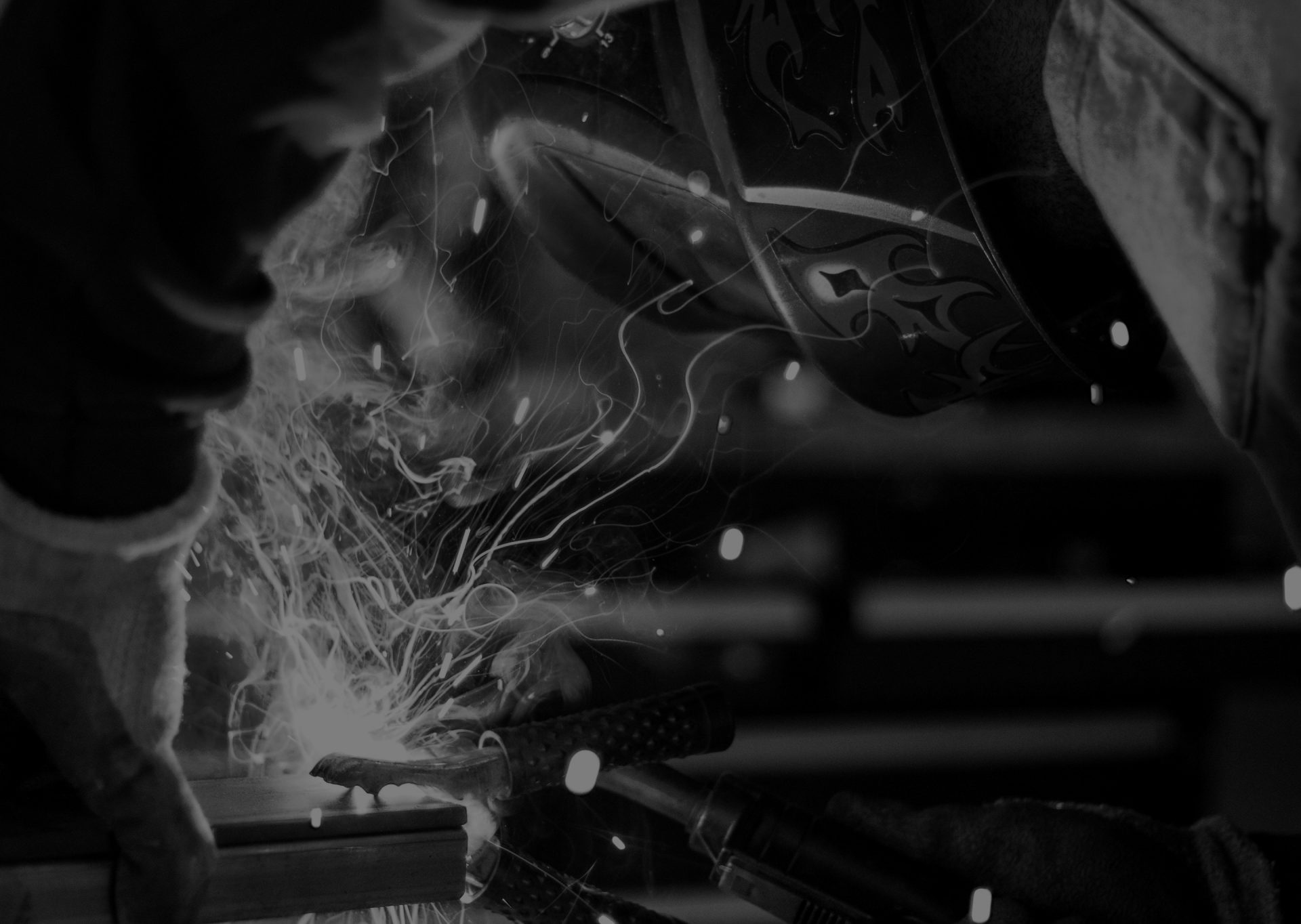
What Digital
Construction
looks like today
The construction industry has been slow to adopt digital technology.
For years, the technology hype ran way-ahead of what was achievable in practice. That is not the case today though. The technologies for digital design and construction are mature, proven and work. In many sectors and countries, a digital approach… Read More
The construction industry has been slow to adopt digital technology.
For years, the technology hype ran way-ahead of what was achievable in practice.
That is not the case today though. The technologies for digital design and construction are mature, proven and work. In many sectors and countries, a digital approach is becoming the norm.
In most markets, we see a transition phase in place with some digital technology being used, within an overall project approach that is still rooted in pre-digital ways of working.
This hybrid approach provides some benefits and allows the industry to change gradually and step-by-step. It does, however, leave a lot of extra risk and cost in the process and adds work because the data doesn’t flow.
For example, if the design process is digital model based, but the main building contractor can only work with traditional drawings, then extra work is generated managing the drawings and lots of opportunities for improved management construction missed.
We see fully digital construction processes working in parts of the construction market, particularly large, complex programmes in countries that have already mastered BIM, and for the more forward-thinking clients. An end-to-end digital construction process is faster and more informed throughout. Off-site, factory built, modular construction is often part of the solution too, with focus on a just in time delivery approach.
Although off-site working has existed long before digital technology came along, a digital approach, using a library of standard components can make for a high-quality build, efficiently and with less time on-site.
For years, the technology hype ran way-ahead of what was achievable in practice.
That is not the case today though. The technologies for digital design and construction are mature, proven and work. In many sectors and countries, a digital approach is becoming the norm.
In most markets, we see a transition phase in place with some digital technology being used, within an overall project approach that is still rooted in pre-digital ways of working.
This hybrid approach provides some benefits and allows the industry to change gradually and step-by-step. It does, however, leave a lot of extra risk and cost in the process and adds work because the data doesn’t flow.
For example, if the design process is digital model based, but the main building contractor can only work with traditional drawings, then extra work is generated managing the drawings and lots of opportunities for improved management construction missed.
We see fully digital construction processes working in parts of the construction market, particularly large, complex programmes in countries that have already mastered BIM, and for the more forward-thinking clients. An end-to-end digital construction process is faster and more informed throughout. Off-site, factory built, modular construction is often part of the solution too, with focus on a just in time delivery approach.
Although off-site working has existed long before digital technology came along, a digital approach, using a library of standard components can make for a high-quality build, efficiently and with less time on-site.
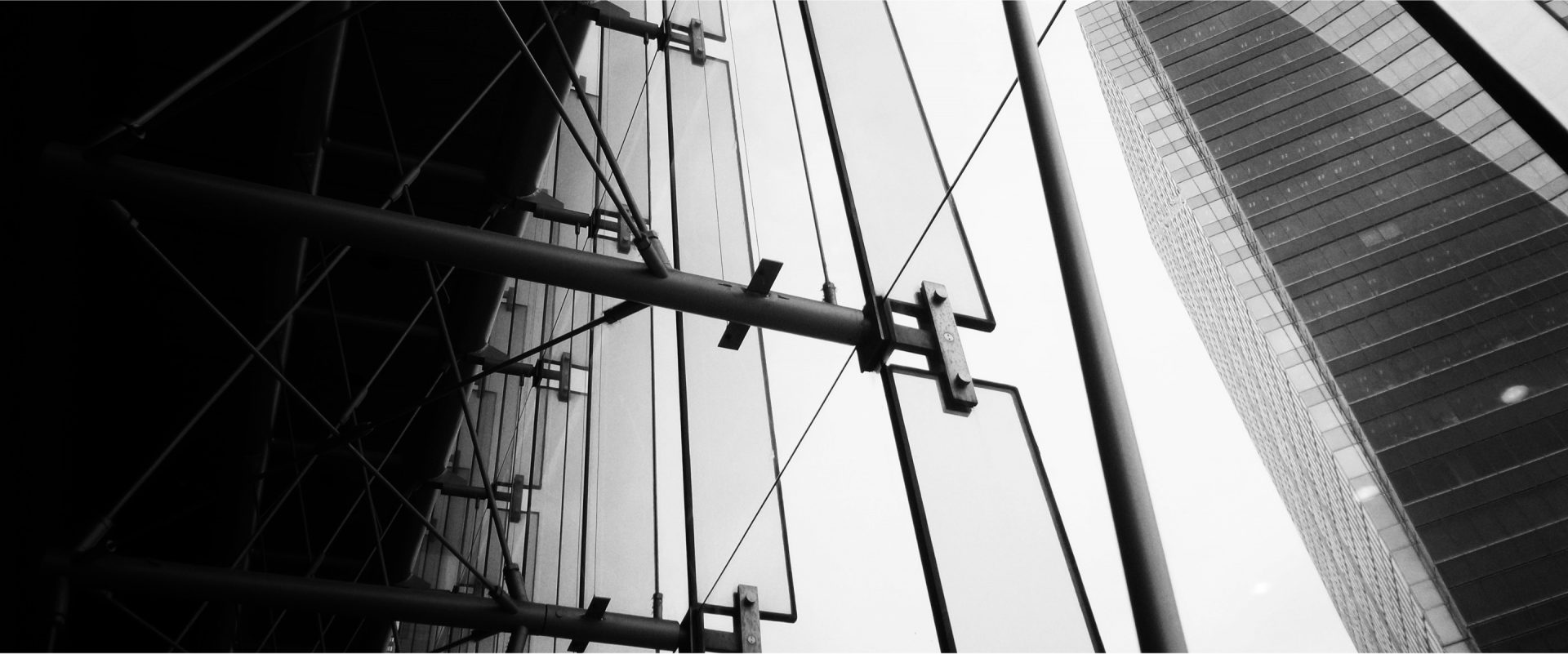
Adoption of Building Information Modelling
Adoption of Building Information Modelling
The foundation for any digital construction process is Building Information Modelling (BIM), so this is a vital piece of the jigsaw puzzle. If your supply-chain can’t work in 3D with a collaborative process (“do BIM”), then 4D or 5D digital collaboration is probably a step too far.
Around the world we see that BIM is now used by most firms in the supply-chain in many countries, with the Nordic countries, UK and USA leading the efforts.
Countries all over the world are gradually adopting BIM because for large government projects it delivers better results. In those countries we typically see most firms in the industry using BIM for at least some of their projects.
We also see many large international commercial clients also adopting BIM and requiring it for all their projects, because it is more efficient and low risk. In 2018, an international standard ISO19650 was agreed for BIM, which will accelerate the trend towards Digital Information Delivery.
The visualisation of a proposed design, with the ability to see what it will look like, is proving a very powerful tool in getting the right design, and in making the construction programme work. The tools and data required to produce visualisations is now widespread and reasonably priced, so we are seeing an explosion in the use of visualisation. For example, McBains used Virtual Reality in the design of a police station; getting the people who would use the building to experience and test out every element of the design.
This applied to the journey through to custody for prisoners and getting the balance of sightlines and privacy right with partitions, so that visitors to the police station would be handled well.
Similarly, a 4D simulation of the construction schedule allowed contractors and sub-contractors, planners and designers to work together to make the design easier to build, and to get the programme right. The use of digital surveying and geolocation technologies for modelling sites, or indeed whole cities is fairly mature.
Most major world cities have been scanned (often multiple times) with multiple companies selling data of a variety of types and accuracies. The price of technology like laser scanners, drones, and photogrammetry (turning photos into 3D models) has come down a long way and continues to fall.
Drone technology makes it fairly easy and cheap to scan a site regularly, though most countries have some regulations requiring registration of certification of the drone pilot. Most importantly, processing and making use of large quantities of survey data has become relatively easy and cheap, thanks to cloud computing.
Bringing time and cost into a BIM process for true 5D digital engineering is still leading edge. 5D is being used for clients that either have large multi-year, multi-project programmes, where the effort required to gather data, define processes and build libraries of re-useable components will pay off.
For example, Deutsche Bahn is using a 5D approach to project managing rail programmes, with some 5,000 projects being managed through a 5D BIM platform. Another example is the UK’s Smart Motorway Programme which is currently changing to a delivery model involving a stable alliance for the whole programme covering design, project management and construction, with shared data, a collaborative approach and a modular digital design.
The foundation for any digital construction process is Building Information Modelling (BIM), so this is a vital piece of the jigsaw puzzle. If your supply-chain can’t work in 3D with a collaborative process (“do BIM”), then 4D or 5D digital collaboration is probably a step too far.
Around the world we see that BIM is now used by most firms in the supply-chain in many countries, with the Nordic countries, UK and USA leading the efforts.
Countries all over the world are gradually adopting BIM because for large government projects it delivers better results. In those countries we typically see most firms in the industry using BIM for at least some of their projects.
We also see many large international commercial clients also adopting BIM and requiring it for all their projects, because it is more efficient and low risk. In 2018, an international standard ISO19650 was agreed for BIM, which will accelerate the trend towards Digital Information Delivery.
The visualisation of a proposed design, with the ability to see what it will look like, is proving a very powerful tool in getting the right design, and in making the construction programme work. The tools and data required to produce visualisations is now widespread and reasonably priced, so we are seeing an explosion in the use of visualisation. For example, McBains used Virtual Reality in the design of a police station; getting the people who would use the building to experience and test out every element of the design.
This applied to the journey through to custody for prisoners and getting the balance of sightlines and privacy right with partitions, so that visitors to the police station would be handled well.
Similarly, a 4D simulation of the construction schedule allowed contractors and sub-contractors, planners and designers to work together to make the design easier to build, and to get the programme right. The use of digital surveying and geolocation technologies for modelling sites, or indeed whole cities is fairly mature.
Most major world cities have been scanned (often multiple times) with multiple companies selling data of a variety of types and accuracies. The price of technology like laser scanners, drones, and photogrammetry (turning photos into 3D models) has come down a long way and continues to fall.
Drone technology makes it fairly easy and cheap to scan a site regularly, though most countries have some regulations requiring registration of certification of the drone pilot. Most importantly, processing and making use of large quantities of survey data has become relatively easy and cheap, thanks to cloud computing.
Bringing time and cost into a BIM process for true 5D digital engineering is still leading edge. 5D is being used for clients that either have large multi-year, multi-project programmes, where the effort required to gather data, define processes and build libraries of re-useable components will pay off.
For example, Deutsche Bahn is using a 5D approach to project managing rail programmes, with some 5,000 projects being managed through a 5D BIM platform. Another example is the UK’s Smart Motorway Programme which is currently changing to a delivery model involving a stable alliance for the whole programme covering design, project management and construction, with shared data, a collaborative approach and a modular digital design.
Off-site and modular systems, reducing construction time and risk
Off-site and modular systems, reducing construction time and risk
Using modules and systems assembled off-site in a factory is a pre-digital idea. For example, Pell Frischmann engineers designed the modular, prefabricated concrete Centre Point Tower in London in 1965, to enable the building on a very small site.
Huf Haus, introduced their iconic factory assembled houses in 1972. Digital makes modular more powerful and flexible, and can connect up the supply-chain in new ways. Moving work from outdoor construction sites to indoor factories, improves productivity and quality.
Using modular systems and designs can also make design faster and easier, although it does require careful planning of the logistics to get modules from the factory to the right place in the construction site. It is a trade-off and will usually increase the cost of materials and logistics, and reduce the labour cost. The biggest benefit is reduced time on-site, and risk of cost and time over-runs. For some owners, their business case process will not evaluate the full, likely cost of the project including risk and therefore, traditional construction will seem cheaper but isn’t in reality. For most projects a mix of on-site and off-site working provides the best solution.
Using modules and systems assembled off-site in a factory is a pre-digital idea. For example, Pell Frischmann engineers designed the modular, prefabricated concrete Centre Point Tower in London in 1965, to enable the building on a very small site.
Huf Haus, introduced their iconic factory assembled houses in 1972. Digital makes modular more powerful and flexible, and can connect up the supply-chain in new ways. Moving work from outdoor construction sites to indoor factories, improves productivity and quality.
Using modular systems and designs can also make design faster and easier, although it does require careful planning of the logistics to get modules from the factory to the right place in the construction site. It is a trade-off and will usually increase the cost of materials and logistics, and reduce the labour cost. The biggest benefit is reduced time on-site, and risk of cost and time over-runs. For some owners, their business case process will not evaluate the full, likely cost of the project including risk and therefore, traditional construction will seem cheaper but isn’t in reality. For most projects a mix of on-site and off-site working provides the best solution.
Our Recommendation
Construction as an industry is changing to adopt digital technology and off-site construction techniques. Over the course of your multi-year project, things will continue to evolve and the benefits over traditional techniques are likely to widen. Some innovations will be more useful and appropriate for some projects than others.
We recommend discussing with your suppliers what is most important for your project and what innovations can be included in your project to help solve those problems.
If you would like to know more please click on one of our sponsors: